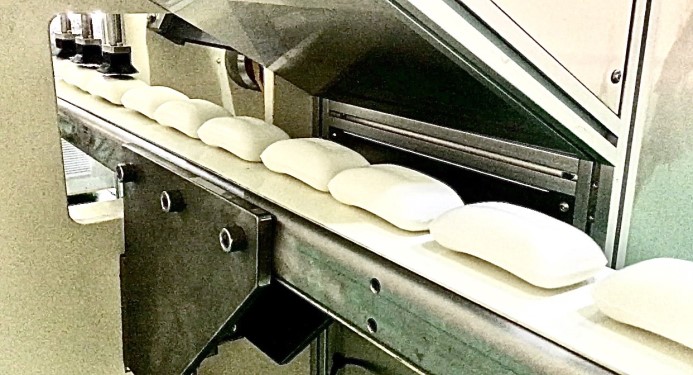
Soap finishing line
Soap Finishing Line
To achieve a standardized production process that complies with modern hygiene and safety regulations, fully saponified, colorless, and odorless soap noodles are used for coloring, scenting, and additive blending.
These ingredients are processed through a series of automated procedures—including mixing, kneading, refining, vacuum extrusion, cutting, and stamping—using specialized equipment.
This ensures a highly efficient and precise fully automated soap production line.
1.Mixer Introduction
Our mixers are divided into two main series: the single-blade mixer BMS series and the twin-blade kneader KMS series.
The inner tanks of all mixers are made of stainless steel. The blades are also precision-machined and cast from stainless steel to ensure durability and hygiene.
Each mixer is driven by a high-efficiency motor and a powerful reducer for optimal performance.
A fully enclosed protective cover and safety switch are included to ensure operator safety.
To operate, materials are loaded into the mixer, the mixing time is set, and the machine is started. The mixing blades break down the materials, allowing colorants, fragrances, and additives to be evenly distributed throughout the mixture.
2. Refiner introduction
Our T-Series pelletizers are available in various configurations—including single-screw or twin-screw designs, and single-layer or multi-layer constructions—to meet different customer processing requirements and production capacities.
All extrusion barrels are made of stainless steel and undergo multiple machining processes to minimize the clearance between the barrel and the screw, ensuring maximum output efficiency and consistent product quality.
The screws are made from hardened aluminum alloy or stainless steel, with multiple models available for different applications. The system is powered by a high-efficiency motor and a robust gear reducer.
During operation, raw materials are fed into the pelletizer. As the screw rotates within the extrusion barrel, pressure is generated to knead and compress the material.
A cooling water circulation system can be applied to the barrel’s outer jacket to maintain temperature stability.
Through the action of a screen and scraper, impurities are filtered out, while the material is refined, homogenized, and formed into uniform pellets.
3.Rolling mill introduction
Our MRS Series Three-Roll Mills are available in either horizontal or inclined roll arrangements, depending on the characteristics of the materials being processed.
All rollers are made of stainless steel and undergo special treatment and precision machining to achieve high hardness and accurate rotational balance.
The machine is driven by a high-efficiency motor and belt pulley system.
A cooling water circulation system can be applied to the internal chamber of the rollers to maintain temperature stability.
The gap between rollers can be finely adjusted according to production requirements to achieve optimal grinding and mixing performance.
During operation, materials are fed into the machine and processed through a two-stage grinding system created by rollers rotating at different speeds.
This allows for uniform dispersion of materials and additives, resulting in excellent mixing and refinement.
4.Plodder/Extruder introduction
Our P-Series extruders are available in various configurations—including single-screw or twin-screw designs, and single-layer or multi-layer constructions—to meet different customer processing requirements and production capacities.
All extrusion barrels are made of stainless steel and undergo multiple machining processes to minimize the clearance between the barrel and the screw, ensuring maximum output efficiency and consistent product quality.
The screws are made from hardened aluminum alloy or stainless steel, with various models available. The extruders are driven by a high-efficiency motor and a powerful gear reducer for reliable and stable operation.
The double-layer extruder can be equipped with a vacuum chamber to extract excess air and moisture during extrusion, ensuring a tighter material bond.
The extrusion head features a jacketed heating design controlled by a thermostat, allowing precise temperature regulation and surface smoothness.
Different die sizes and shapes can be customized according to customer requirements, enabling diverse product outputs.
During operation, raw materials are fed into the extruder, where pressure generated by the rotating screw kneads and compresses the material.
A cooling water circulation system can be applied to the outer jacket of the barrel to maintain temperature stability.
A filtering screen helps remove impurities and ensures refined mixing.
Finally, the material is compressed and extruded through the extrusion head and die into continuous strands, ready for further processing.
5.Soap Cutter introduction
Our PCC Series Soap Cutting Machines can be configured to suit different production lines, and are available in single-line and dual-line models.
The S-type high-speed models are equipped with PLC control systems and touchscreen interfaces for easy operation.
A fully enclosed protective cover and safety switch are included to ensure operator safety.
Cutting length can be easily set via the touchscreen, and the machine is driven by a high-performance servo motor for ultra-high-speed cutting.
Optional features include a printing system and customized soap stamps or embossing rollers, allowing logos and product names to be imprinted directly onto the soap.
These customizable features help enhance product diversity and branding.
6.Stamper introduction
Our printing machines are categorized into two series based on product characteristics and production capacity requirements: the DST Series Rotary Stamper and the PPR Series Vertical Press Stamper.
DST Series – Rotary Stamper
The DST Series is ideal for bordered soaps with high moisture and stickiness.
Soap bars are conveyed into the machine via a conveyor belt. A pusher plate automatically guides the bars into the mold frame, where the upper and lower dies shape the soap and emboss the logo and product name. Finished products are then transported out by the conveyor.
The system features a patented cam design, driven by a high-efficiency motor and a powerful reducer. A fully enclosed protective cover and safety switches ensure operator safety.
Inside the machine, temperature controllers and solenoid valves automatically regulate air circuits and mold temperatures. Integrated computer control and monitoring systems ensure consistent product quality and stable production output.
PPR Series – Vertical Press Stamper
The PPR Series is suitable for a wide range of soap shapes. Its multi-cavity mold design significantly improves production efficiency.
Soap bars are fed into the machine via a conveyor belt. A robotic arm equipped with vacuum suction cups positions the bars at the center of the lower mold.
The upper and lower dies then shape the soap and imprint logos and names. Finished products are trimmed using a scraper to remove excess material before being conveyed out of the machine.
This series also features a patented cam design, driven by a high-performance servo motor and heavy-duty reducer.
A fully enclosed safety cover and safety switches protect the operator.
Photoelectric sensors detect material status, while temperature controllers and solenoid valves manage air pressure and mold temperature. These functions are integrated with a computer-controlled monitoring system to ensure high-quality output and stable production flow.